Дата публикации: 12.09.2024
Студентка ОмГТУ Евгения Архипенко создала уникальную разработку, которая позволит в режиме реального времени и без помощи человека отслеживать брак на производстве полимерных изделий. Прибор контроля дефектов в ближайшее время пройдёт испытание на производстве. И в случае подтверждения своей эффективности может стать успешным коммерческим продуктом. Запрос на студенческую разработку огромный. Только в России сегодня работает более 60 заводов по производству ПВХ-профиля, которые смогут с помощью прибора экономить миллионы на раннем выявлении брака.
Разработку уже по достоинству оценили эксперты международных конкурсов, среди которых НТСИ-SkАРТ и «Мы – интеллектуалы XXI века». А недавно прибор был представлен на конкурсе студенческих стартапов, где был удостоен гранта в размере миллиона рублей, поэтому работа над его усовершенствованием и внедрением в жизнь продолжится.
Как родилась идея создания инновационного прибора, как он позволяет выявлять брак полимерных изделий и какое будущее сулит производителям?
Путь в мир технологий Евгения начала на первом курсе. Ей предложили принять участие в «Турнире Трёх Наук».
«В качестве руководителя команды выступал Александр Тигнибидин. Именно он мне и рассказал о студенческом конструкторском бюро “Микрон” (СКБ), в которое я позже вступила. В СКБ обратился директор завода по производству ПВХ-профилей. Проблема заключалась в том, что при нарушении параметров производственной линии на выходе получается профиль с геометрическими дефектами. Стояла задача снизить брак. Так и возникла идея создания прибора».
Сейчас пластиковые окна изготавливают из ПВХ-профиля. Его получают путём экструзии – жидкий пластик продавливается через специальную головку. Калиброванный профиль охлаждается, маркируется и нарезается шестиметровыми брусками. Каков будет процент брака, предугадать сложно. Отследить его в режиме реального времени пока нельзя.
«За данным процессом следит и регулирует технологические параметры оператор, который в связи с различными человеческими факторами не может разглядеть небольшие дефекты. Как раз эту проблему и решает наша разработка. На данный момент на российском рынке проводится только послеоперационный контроль с помощью универсальных средств измерений в лаборатории предприятия. Внедрение активного контроля на производстве является инновационным», – поясняет Евгения.
Работа над инновационным прибором началась в мае 2022 года. В команде с Евгенией Архипенко – выпускник ОмГТУ Максим Рухлов и научный руководитель студенческого конструкторского бюро «Микрон», доцент кафедры «Нефтегазовое дело, стандартизация и метрология» Александр Тигнибидин. Девушка уверяет: половая дискриминация в коллективе отсутствует. Каждый выполняет свою задачу.
«Мы разделили задачи так, чтобы максимально эффективно использовать наши сильные стороны. В мои задачи – как руководителя проекта – входит планирование работы, участие в переговорах с инвесторами и партнёрами, разработка стратегии развития. Максим отвечает за электронную часть прибора, а именно работу по созданию интерфейса на сенсорном дисплее, создание меню управления и алгоритм обнаружения дефектов. Научный руководитель – Тигнибидин Александр – проверяет качество выполненной работы и подсказывает то, как можно улучшить конструкцию».
Здесь и сейчас
Евгения предложила идею прибора, который сможет отслеживать геометрию ПВХ-профиля в процессе производства в режиме реального времени. О дефектах он должен автоматически сообщать оператору. Своевременный контроль брака поможет сэкономить миллионы рублей в год, говорят авторы разработки.
«Расчёт проводился исходя из объёма бракованной продукции и её себестоимости. Также учитывали среднюю ежегодную статистику по возврату бракованных изделий, отправленных заказчикам в другие города».
Опытный образец прибора создан. Для этого были использованы технологии 3D-печати. Разработку уже успели оценить эксперты международных конкурсов, среди них НТСИ-SkАРТ, «Мы – интеллектуалы XXI века». Призовые места и положительные отзывы собраны.
«Эксперты высоко оценили идею проекта, задавали интересные уточняющие вопросы по проекту. Например, вопрос возник по поводу количества измерительных датчиков. В нашем проекте используется один с функцией вращения вокруг изделия. Эксперт предложил использовать четыре неподвижных датчика. Это усложнит конструкцию и калибровку прибора, но мы взяли эту рекомендацию как запасной вариант».
Миллион на техночудо
Самая главная победа завоёвана недавно. Прибор контроля дефектов был представлен на конкурсе студенческих стартапов. Разработка удостоена гранта в миллион рублей, а значит, работа над ней продолжится. Цели поставлены.
«Мы расписали календарный план по разработке прибора на год. Это разработка бизнес-плана стартап-проекта в соответствии с установленными требованиями, создание сайта, а также создание прибора и проведение производственных испытаний. Деньги с гранта пойдут на создание MVP, создание юридического лица, закупку материалов и комплектующих, а также необходимого оборудования. Прибор будет сделан из более устойчивых и прочных материалов».
В ближайший год опытный образец будет доработан. После в планах – опытные испытания на Омском заводе по производству ПВХ-профилей. Напомним, предприятие изначально направило обращение на разработку, из которого и родился проект.
«За 12 месяцев необходимо выполнить намеченный календарный план. В процессе работы над проектом мы сформируем дизайн прибора и интерфейс управления на дисплее».
Испытания на производстве помогут превратить студенческую разработку в коммерческий продукт. Запуск на рынок и реальные продажи – в перспективе. Запрос есть. В России работает более 60 заводов, которые производят ПВХ-профиль. Прибор может быть внедрён на предприятиях. Возможен выход на зарубежный рынок, например, Китай.
Автор: Ксения Тоичкина
Фото: личный архив Евгении Архипенко
Читайте также
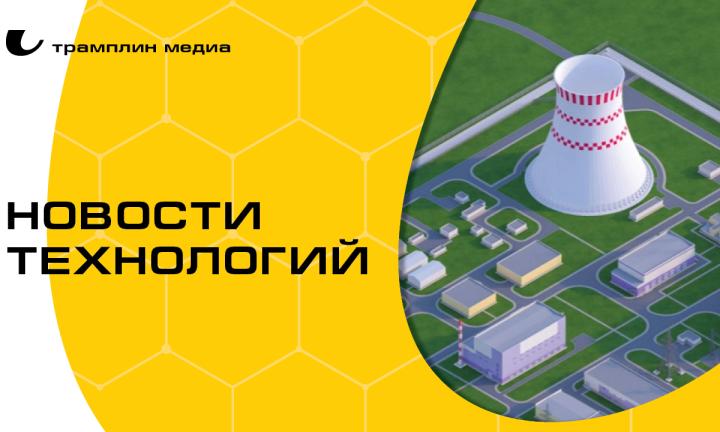